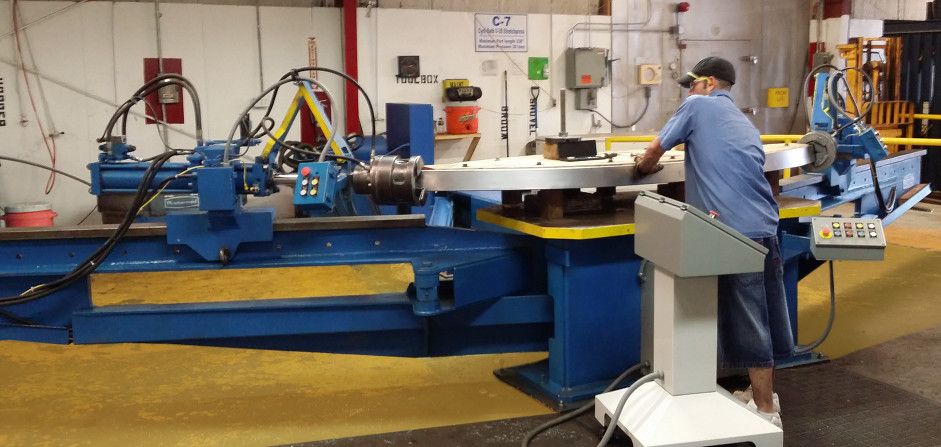
The Stretch Forming Process
Stretch-forming is a method of forcing metal parts such as, steel shapes, aluminum extrusions and sheet metal, into permanently curved shapes of predetermined contour.
A simple explanation of the process; a straight piece of aluminum is gripped at each end by a pair of Collet Jaws then stretched into a state of tension. As the piece remains at tension it’s wrapped around a contoured form block, or die, that has been created to match the desired shape of the finished product.
If a part were to be curved without first being stretched, two natural forces would occur during the process. First, one half of the part would naturally be stretched. Secondly, the other half would go into compression, and the neutral axis would be the division between the two. Stretching the material compensates for the compression that would normally take place on the inner surface of the part, which, in turn, eliminates the wrinkling or twist.
It could be said that a stretch-forming machine bends parts into curved shapes, but does so while pulling the wrinkles out of the part before they can occur.
In this combination, bending and stretching, the outer fibers of the part being formed experience an elongation stretch sufficient enough to put this fiber into yield i.e. it has been stretched beyond it’s ability to return to it’s original length after the stretching force has been relaxed. Therefore, the parts remain close to the shape of the form block after it’s been removed from the stretch-forming machine.
The stretching action taking place in the stretch-forming process not only eliminates wrinkling but also helps to eliminate “spring-back”, of the part from the desired finished contour.
Stretch-forming is commonly used in the curving of aluminum sheet, extruded profiles, stainless sheet, bent or rolled profiles, structural shapes, various steel alloys, brass, bronze, copped, titanium and even Inconel. It allows the curving of true radius contours, ellipses, compound bends, helical bends and can included straight legs.
Although it is a cold form of bending, heat can be introduced in the stretch forming process to allow for bending of exotic alloys.
The Stretch Wrap Forming Machine
The typical machine that does this type of work is composed of a central table for mounting the form block and two arms. A hydraulic tension cylinder is attached to each arm, and in turn, each of these cylinders is connected to a gripper jaw. The arms pivot by the action of the other hydraulic cylinders. Therefore, when a straight extrusion is gripped in the jaws it undergoes the initial stretching necessary to eliminate the expected inner wrinkling. It is then curved around the form block by actuating the arms, while remaining in a state of tension.
Techniform has a large assortment of stretch form equipment with capabilities of forming extruded profiles up to 22" circle size, up to 45' stock lengths, as well as skins and steel profiles.
Industries and History
Stretch Forming is used extensively in the aerospace, marine and ship-building industry. Since the introduction of stretch forming its primary use has been the forming of aircraft skins, cowls and air frame components. Later, as machines were developed and became larger and more powerful, the technology was adapted to forming of boat and ship hulls along with various other components.
Because of the quality of the stretch forming process it has been adapted over the years to the automotive industry, rail car and industrial manufacturing; such as conveyors and equipment manufacturing.
Eventually the process would be pioneered for the architectural industry and opened up architects to possibilities of curved facades, architectural details and roof lines previously not possible. Large curved glass facades were now possible, as the process is a perfect match for the curving of large curtain-wall systems.